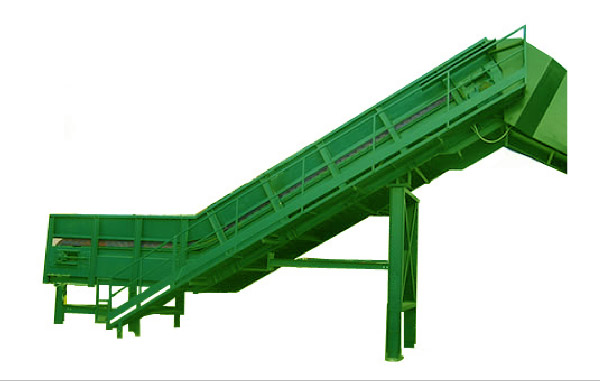
The primary function of magnetic chip conveyors is to remove metal chips from the production floor quickly and efficiently. Metal chips produced during machining can be sharp and small. They are also difficult to transport, particularly when the metal chip needs to be moved over a long distance or to an area that is hard to reach. Magnetic chip conveyors utilize powerful magnets embedded in the conveyor belt to attract and hold the metal chips as they move along the belt. This magnetic force ensures that even the smallest and sharpest metal particles are securely transported without the risk of them falling off or becoming dislodged. By using a magnetic field, these conveyors make it possible to move large quantities of metal waste without the need for manual handling, reducing the time and labor involved in the cleaning process.
Magnetic chip conveyors are also adaptable. The systems are customizable to meet the needs of an organization, depending on how many chips they produce, their layout, and operational requirements. Magnetic chip conveyors come in various configurations, including flat, inclined, and even spiral designs, allowing them to be used in multiple settings. For example, in environments where space is limited or where chips need to be moved vertically, inclined magnetic conveyors can be used to transport materials upward or to different levels within a facility. It is possible to adjust the strength of magnetic field in order to handle different sizes and weights. This allows businesses to customize their solution for material handling.
Magnetic Chip Conveyors are versatile and reduce maintenance costs. Traditional conveyor systems often rely on friction to move materials, which can lead to wear and tear on the conveyor belt and other components. This friction also increases the likelihood of jams, misalignment, and material spillage. Magnetic chip conveyors, on the other hand, minimize friction because the magnets secure the materials without direct contact with the conveyor belt. The belts will wear less due to the reduced friction, which means fewer repairs for the system and longer life. The continuous, smooth movement of materials also reduces the risk of interruptions in production, keeping the manufacturing process running smoothly without costly delays. Magnetic chip conveyors are a low-maintenance, reliable solution for industries that require high-volume and high-speed production. They help optimize workflows and reduce downtime. To get added details please check out the post right here
,aspect=fit)
Magnetic chip conveyors not only improve operational efficiency but also workplace safety. Metal chips, particularly those produced in high-volume machining processes, are often sharp and hazardous. Unchecked metal chips can cause dangerous conditions in the workplace by building up on the floor of the factory, causing slips, falls, and trips. Magnetic chip conveyors automate the removal and transport of these metal chips, reducing the need for workers to manually handle potentially dangerous materials. This not only minimizes the risk of injury but also helps maintain a cleaner, safer work environment. Moreover, by preventing metal chips from being scattered around the production area, these conveyors reduce the risk of fires or other safety hazards that may arise from the accumulation of flammable oils or debris.
Magnetic chip conveyors also offer a high level of sustainability. In industries that generate a large amount of metal waste, such as machining and automotive manufacturing, recycling these materials is often a priority. Magnet conveyors can sort and collect metal chips that are then recycled or reused. This reduces waste and conserves valuable resources. These conveyors help to reduce waste by separating ferrous metals and other materials. They also make it possible to recycle the metals. Additionally, the longer lifespan and lower maintenance requirements of magnetic chip conveyors help reduce the environmental impact of material handling systems. These systems require fewer repairs and replacements, which reduces waste. They are also more environmentally friendly for industries who prioritize sustainability.